Tucked away in a small corner of one of Britain’s most stunning national parks, one of the world’s most innovative and challenging tunnelling projects is in full-swing.
After years of planning, the idea to build a mine with multiple shafts up to a mile-deep under heavily protected moorland came to fruition on one condition – that the mine itself was connected to its processing and distribution facilities through a 40km underground tunnel, up to -360m underground.
Tunnelling, is by its very nature a high-risk activity and whilst it is no longer deemed as new technology, this particular project presented us with some very unique challenges, unseen before on a world-scale. Having robust Emergency Preparedness and Response arrangements in place was and still is critical.
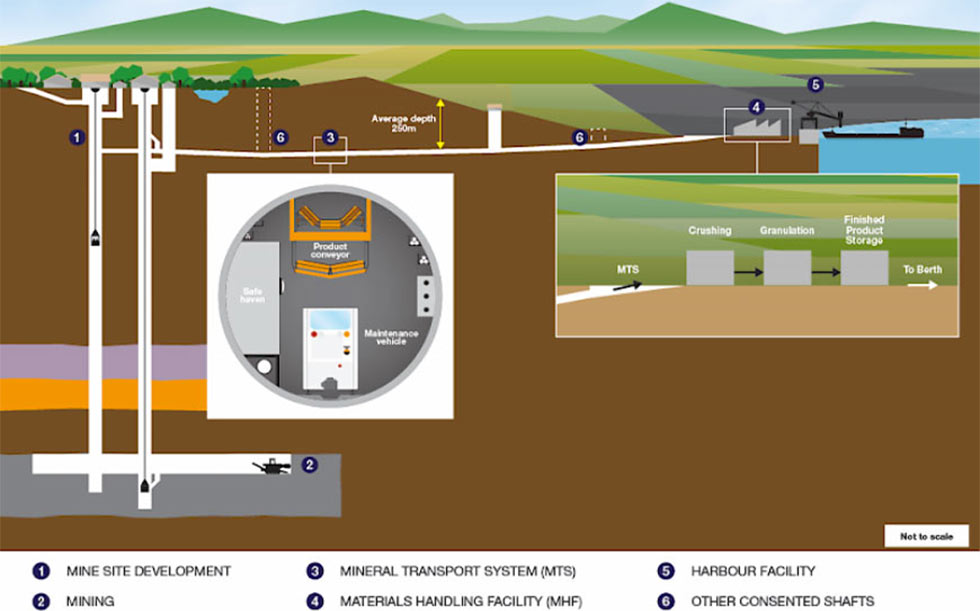
Overview of the Woodsmith Project
Working closely with the principle tunnelling contractor – Strabag, we regularly train and exercise in the tunnel environment. This very specific training is aligned to pre-defined scenario specific emergency pre-plans and ensures compliance with the appropriate regulations and legislation.
Excavation for the Mineral Transport System (MTS) started in early 2019 with the launch of the first of two Tunnel Boring Machines (TBMs). The polyhalite resource, a mineral that will be mined by Anglo American near Whitby, is located 1,600m beneath the North York Moors National Park, and once extracted will be lifted to an underground cavern to transport to the Teesside processing plant and export shipping harbour on the Teesworks site via the 40km long Tunnel.
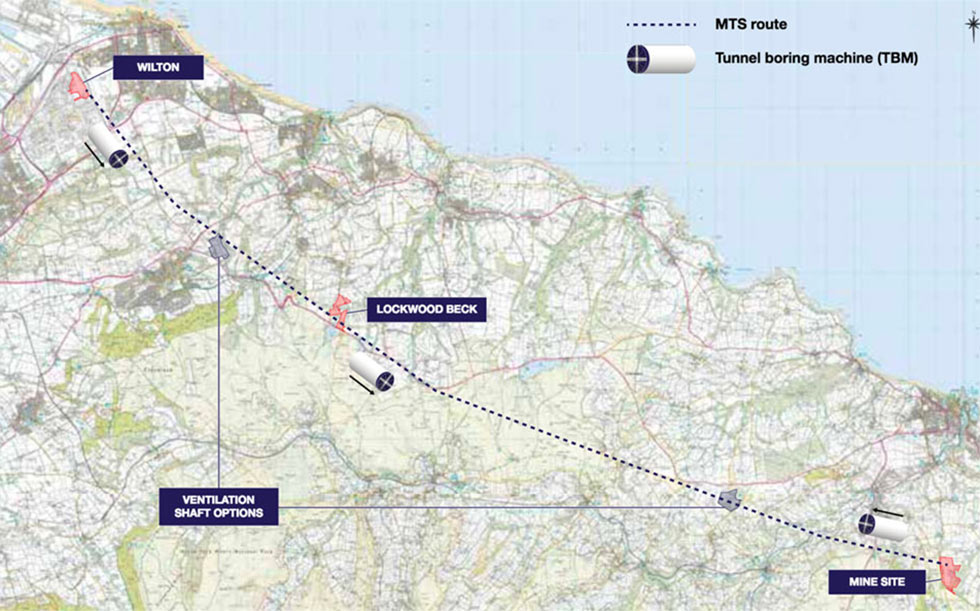
Route of the Mineral Transport System (MTS)
The first TBM, a machine supplied by Herrenknecht, is proceeding on a down gradient slope from the portal at Wilton International and will travel to the intermediate shaft cavern at Lockwood Beck. The same TBM is planned to progress from the Lockwood Beck shaft towards the mine head with a second TBM, on a third drive, progressing from the mine head towards an in-tunnel junction to complete the remaining reach of the MTS tunnel.
Geotechnical profile along the TBM drives of the mineral transport system
We work closely with Strabag to understand the the potential risks associated with a drive of this distance and at such depths. We used data from historical and recent mining activities that are available to help improve the understanding and control of the geological conditions which impact on emergency preparedness and response arrangements.
Cross section of the TBM excavation operation
The 6m diameter Herrenknecht TBM tunnel is lined to 4.9m with concrete segments reinforced with steel rebar cages which are specifically designed to take the overburden pressure and up to 29 bar of hydrostatic pressure.
The concrete segments are transported into the tunnel using a single service rail track heading that supports logistics within the tunnel – including emergency access and egress via locomotives which rely on movable and fixed California crossings – including dedicated specialist ‘Rescue Trains’.
This comprehensive amount of industrial scale equipment, along with the TBM itself provides a range of challenges, which is why it is imperative that we have the right equipment to deal with any emergency situation within the tunnel at any time – Which we ensure that we do.
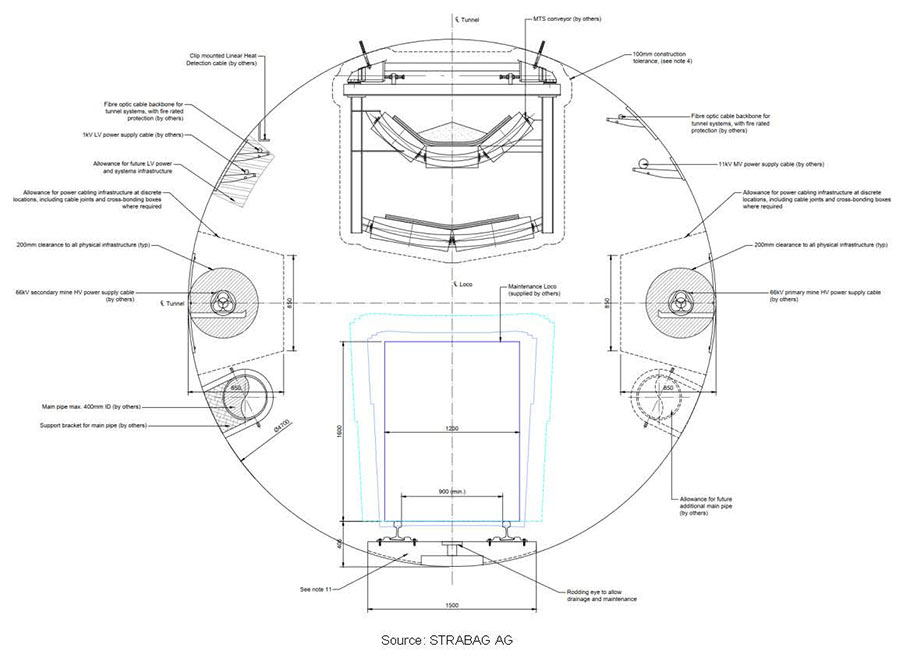
Cross section of the permanent mineral transport conveyor system
After launching in June 2019, advance rates to date have been high. With this high performance, the project is ahead of schedule, however as the project advances, the risk increases – becoming one of the longest and deepest single bore tunnels in the world presents unique challenges.
To address this, we are working on innovative solutions to help mitigate any incident, in the unlikely event one may occur.
Please contact us for further information.